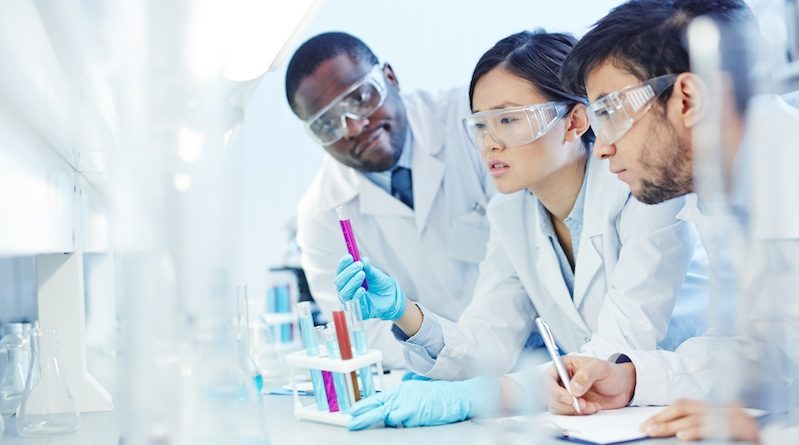
Leading the way to clean and affordable polymers
Total’s ambition for 2035 is to be the responsible energy major. In practical terms, that means providing energy that is affordable, reliable and clean. Total’s petrochemical activities play a key role in achieving this ambition.
We develop, manufacture and market polymers that are used in the packaging, automotive, construction, household appliances and medical sectors. As the second largest European petrochemical producer, we are active in polyethylene, polypropylene and polystyrene which represent more than 60% of the global demand for plastics.
World population growth and the indisputable added value of plastics drive an average growth of 3% per year for these materials. Their use significantly reduces carbon emissions compared to many alternative materials.
Nevertheless all stakeholders of plastics must come up with the solutions to decrease plastics’ environmental footprint in order to meet the growing demand while limiting climate impact. As a pioneer in developing innovative polymers, Total intends to lead the way in the new circular economy of its polymers.
Polymers, built-in advantages to reduce the environmental impact of products
Plastic has a built-in advantage when it comes to reducing the carbon footprint of products because it is lighter than other materials such as glass and metal. Increasingly, metal automotive parts are being replaced by lighter composite materials, which reduce fuel consumption and, ultimately, carbon emissions. Cutting a vehicle’s weight by 200 kilograms reduces fuel consumption per 100 kilometers by 0.5 liters.
Our researchers have developed technologies that further reduce the use of polymer materials.
Our Lumicene range of packaging films, for example, are 25% thinner but just as strong as conventional films, and our Excell-R for insulation reduces the amount of product needed by 20%.
We are also developing renewable, biobased and recycled raw materials for plastics.
Total Corbion PLA, 2nd largest global producer of bioplastics
Total and Dutch company Corbion are building a plant in Thailand to produce polylactic acid (PLA), a biobased polymer made from sugar or starch. PLA is part of tomorrow’s solutions: biodegradable, bringing a wealth of new functional properties like all invented thermoplastics have brought.
With a capacity of 75,000 tons per year, the facility will make Total Corbion PLA the world’s second largest bioplastics company.
Total, a pioneer in plastic recycling
We have made plastic recycling a priority in our developments for a number of years. The work carried out at our research center in Feluy, Belgium, will broaden the market for recyclates by adapting their properties. Despite sorting and recycling, current recyclates contain a mixture of products.
As a result, average properties do not meet the technical requirements for many applications. The approach taken by our product development teams consists of adding a designed amount of booster per recyclate type.
Boosters are specific virgin materials developed by R&D teams leveraging our technological expertise in catalysis and polymerization processes. The boosted properties combined with the average properties of recyclates allow us to meet customer specifications.
We have thus produced polypropylene and polyethylene grades containing at least 50% recycled materials that perform just as well as virgin polymers. These grades are currently being qualified by our customers.
We have also achieved a world first in polystyrene: industrial-scale production of polystyrene
containing a significant percentage of recycled packaging while delivering optimum performance.
Wide scale plastic recycling will require everyone’s participation across the value chain
We are working in close cooperation with recyclers to streamline the different stages of the manufacturing process and ensure performance that can be consistently repeated.
We are enhancing the performance of booster/recyclate blends with partner customers that are committed to reducing the environmental footprint of items manufactured.
Everyone across the value chain must take part if we are to achieve the ambitious objectives set out in the European Union’s circular economy roadmap.The required investments are vast for a value chain facing a challenging economic environment.
The E.U.’s sorting and recycling capacity must be increased and technology must be developed to improve recyclate performance for downstream businesses at an acceptable cost.
In order to recycle 50% of plastic packaging within seven years, we will have to expand collection across the E.U. and develop sorting and recycling tools that can handle products not yet recycled in sufficient quantities.
Although by nature a local activity, recycling will have to become an integral part of the European plastic market and meet standards that guarantee performance, quality and reproducibility for the downstream market.
Given the high cost of recycling operations, incentives – for example incentives linked to carbon emissions reduction will be necessary to encourage the use of recycled materials in manufacturing.
The need to reduce pollution in rivers and oceans and to optimize resources must foster our drive to bring landfill plastic waste to an end. Scaling up recycling is the preferred option, but waste-to-energy will also be nec- essary for complex waste that is difficult to recycle with an acceptable environmental