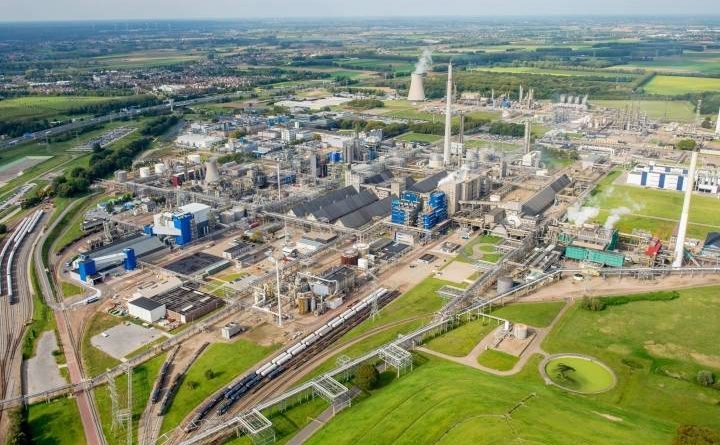
Chemelot – The place to be
Basic chemistry forms the fundament of many economic value chains, just as plankton does within many food chains. Fertilizer, clothing, medicine… none of these would exist without the raw materials that chemistry provides.
The Dutch Minister of Economic Affairs and Climate declared the basic industry to be “crucial” in his vision of sustainability, published recently. The Minister emphasized the indispensable role that the chemical sector plays in the Netherlands, which is factored into his economic policy accordingly. The Dutch Government aims to become – in its own words – “the place to be” for sustainable primary industries in the future.
This is great news, because one of those places to be is the Chemelot chemical complex in South Limburg, the geographical heart of the Meuse-Rhine Euregion and the Antwerp-Rotterdam-Rhine-Ruhr Area (ARRRA). The region is already one of the most highly concentrated areas of chemical companies in the world, accounting for around 40% of Europe’s chemical production.
In view of the Dutch Government’s firm ambition, we should aim to maintain and strengthen that position. Chemelot is a global-oriented chemical site; about 90% of all products produced here are for export.
Chemelot is uniquely positioned to transform into a circular, sustainable, and completely climate-neutral chemical site. Historically the 60+ plants at Chemelot are highly integrated. A product produced in one factory is used as a raw material in another – reducing energy loss and boosting efficiency at the same time. Integration and intense cooperation are key to achieving sustainability and circularity.
The role of chemistry is undisputed; society needs the primary chemical products, both now and in the future. To continue to play this vital role in a socially responsible way, there are two challenges that we face: 1) the raw materials (input) must be renewable (non-fossil), so that the products (output) are also green, and 2) we must electrify all chemical processes, and use electricity from renewable sources.
These two challenges are enormous, but they certainly can be overcome. Currently, raw materials are still being widely produced from fossil fuels at Chemelot; roughly 4 million m3 of natural gas and about 93,000 barrels of naphtha (distillate of crude oil) are consumed each day. Electricity consumption is around 2 million MWh per year. Yet, Chemelot can become 100% sustainable and circular by 2050. There is still a lot of work to be done, and we are on our way.
A prime example is the new factory being built by SABIC and Plastic Energy on the Chemelot site. This new plant will chemically recycle plastic waste and will be in operation in 2021.
Plastic Energy has developed a special technology as part of this collaboration, which melts plastic waste and breaks it down into pyrolysis oil in an oxygen-free environment.
This plastic waste oil is then used by SABIC as a raw material in the existing naphtha crackers, and converted into ethylene and propylene.
This new technology creates a cycle by transforming plastic waste into high-quality raw materials for the production of plastics independent of naphtha. This innovative development will reduce the waste being incinerated, and offers a more environmentally friendly alternative for processing mixed plastic waste.
The use of chemical recycling is a great example of how to make value chains circular and increases cooperation within the circular chain. In this case, companies like Unilever have been actively involved from the outset, as these plastics can be used for food packaging.
We are very proud of this development, which eliminates the need for naphtha originating from fossil fuels, replacing it with a circular alternative. This technology is very progressive and way ahead of other sustainable developments in the world.
But there is a lot to be done before we can apply these and other technologies on a bulk industrial scale. One day Chemelot will run out of space for storage and processing plastic waste, municipal waste, and biomass. However, all recycling factories do not necessarily have to be built on Chemelot; they can be built elsewhere. After the recycling process, renewable raw materials such as pyrolysis oil are transported via existing or new pipelines, water, rail, or road to Chemelot.
Chemelot is a natural hub for various types of infrastructure: pipelines, highways, waterways, rail tracks, and electricity lines.
This infra-structure plays a crucial role in developing a sustainable chemical site, because the pipelines are needed not only to supply the pyrolysis oil, but also to replace the other important raw material: natural gas.
Naphtha and natural gas will slowly but surely be replaced with renewable alternatives. Chemical processes need heat, which is now often generated by burning natural gas. High temperatures will still be necessary for pro- cesses in the future, but the heat will need to be generated from a sustainable electrical source. This means electricity consumption will increase approximately four-fold by 2050.
Within the wider climate debate, Chemelot and the companies on site are certainly not just part of the problem, but they are absolutely an indispensable part of the solution. Chemelot is seeking partnerships on several fronts with relevant companies, knowledge institutes, and governments to help achieve its ambitions – from building infrastructure and obtaining a sufficient amount of green electricity, to creating a level playing field in Europe and across the world. For a chemical site that sells 100% of its products on the world market, the importance of a level playing field cannot be understated.